A public address power amplifier is one of the core equipment in a public broadcasting system, and its quality directly affects the broadcasting sound quality and coverage. As a professional manufacturer of public address equipment, we understand the importance of power amplifiers, so we will discuss how to ensure the production of quality power amplifiers from various aspects.
Selection of Materials
The selection of high-quality components is a priority. The balance between high-quality and cost-effective components needs to be accurately evaluated for different customer needs.
Electronic Components
- Resistance:
High accuracy: ±1% or less
Low noise
Good temperature stability
Recommended Brands: KOA, TE Connectivity, Molex
- Capacitors:
High-quality polyester, polypropylene, or ceramic materials
Stable capacity with low deviation
Low ESR (Equivalent Series Resistance)
Recommended brands: Panasonic, Rubycon, Samsung Electro-Mechanics
- Inductance:
High saturation current
Low core loss
High accuracy and stability
Recommended Brands: Coilcraft, TDK, MURATA
- Diodes and Transistors:
Low forward voltage drop
High switching speed
Low reverse leakage current
Recommended Brands: Fairchild, Infineon, STMicroelectronics
- Integrated Circuits (ICs):
High-Performance Amplifiers
Stable gain and noise figure
Good thermal performance
Recommended brands: Analog Devices, Texas Instruments, STMicroelectronics
- Heat Sinks:
Large surface area for efficient heat dissipation
High thermal conductivity
Good mechanical strength and stability
Recommended brands: Cooler Master, Zalman
- Power Filters:
Low insertion loss
High common mode and differential mode rejection ratio
Good insulation performance
Recommended Brands: PHOENIX CONTACT, Weidmuller, Schneider Electric
- Switches and Relays:
Long life and low contact resistance
Fast switching capability and low jitter
Good electrical and mechanical properties
Recommended brands: Omron, Siemens, Panasonic
- Connectors and Wires:
Highly reliable connections and low resistance
High-temperature and corrosion-resistant materials
Compliance with safety standards
Recommended Brands: Amphenol, Molex, TE Connectivity
- PCB (Printed Circuit Board):
High-quality materials and manufacturing processes
Good insulation and layout design
Compliance with safety standards and impedance control requirements.
Recommended Brands: Taiyo Yuden, Unimicron, Elpress
Magnetic Material
The requirements of high-quality amplifier and player on magnetic material are mainly reflected in the following aspects:
- High Permeability: To obtain better signal transmission and amplification, magnetic materials need to have high permeability. Materials with high permeability can better transmit the magnetic field, reduce magnetic loss and heat loss, and improve the efficiency of the amplifier.
- High Saturation magnetic induction strength: saturation magnetic induction strength determines the magnetic induction strength of the material under a strong magnetic field, and materials with high saturation magnetic induction strength can withstand greater current and magnetic field strength, improving the output power and stability of the amplifier.
- Low Coercivity: coercivity determines the difficulty of demagnetization of the material, low coercivity material can better eliminate the residual magnetism, to ensure the performance and stability of the amplifier.
- High Curie Temperature: Curie temperature indicates the critical temperature for the disappearance of the material’s magnetism, and materials with high Curie temperature can maintain magnetic stability at higher temperatures, thus improving the adaptability of the amplifier’s working environment.
- Low Resistivity: resistivity affects the eddy current loss of the material under a high-frequency magnetic field, low resistivity material can reduce the magnetic loss and heat loss, and improve the efficiency and service life of the amplifier.
In addition, choose magnetic materials with excellent magnetic properties, such as ferrite and NdFeB.
Quality Housing Material
The amplifier’s enclosure material is made of galvanized iron instead of iron for several reasons:
- Anti-corrosion: Iron tends to rust easily when it comes into contact with oxygen and moisture in the air, causing the surface of the housing to become rough, which affects its aesthetics and service life. The galvanized iron shell can provide better corrosion resistance, because the zinc layer can prevent direct contact between iron and the external environment, thus protecting the internal iron from corrosion.

- Aesthetics: galvanized iron can make the surface of the amplifier casing’s silver-white metallic luster, more beautiful than the deep black color of pure iron. At the same time, because the zinc layer has good ductility and plasticity, can also form a variety of different textures and patterns on the surface of the shell, to further enhance the aesthetics.
- Strong Adhesion: the bond between zinc and iron is strong, which makes the galvanized layer not easy to fall off or peel off. This ensures that the amplifier enclosure maintains a better appearance and corrosion resistance during use.
Manufacturing Process
The assembly process of the PA amplifier is a rigorous process that requires strict adherence to operational procedures and quality control points to ensure the performance and quality of the final product. The following are some general requirements for them:
Operation Process
As a professional power amplifier manufacturer, we have a whole set of strict production processes, the following are some of the areas that need special attention:
Preparation Stage
Prior to assembly, all parts must be meticulously counted, checked, and cleaned to ensure their integrity and cleanliness. Simultaneously, it is essential to clean and organize the working environment, ensuring a neat and hygienic assembly environment.
Circuit Board Assembly Stage
When assembling the circuit board, it is necessary to weld the electronic components to the circuit board by the drawings and process requirements. In this process, it is necessary to pay attention to the direction, polarity, and welding quality of the components to ensure that the components are installed correctly, solder joints are firm, and there are no false welds, short circuits, and other phenomena. Component soldering notes are as follows:
- Selection of high-quality environmentally friendly solder and flux: According to the materials and specifications of the components, select the appropriate solder and flux. Some well-known brands such as ATLANTIC, TDK, Murata, and Vishay are recommended. These brands offer a wide range of products including various types of solder and soldering aids with good quality and reliability.
- Control soldering temperature and time: Soldering temperature and time are important factors affecting the quality of soldering. Too high a temperature may result in component damage or poor solder joints, while too low a temperature may result in poor or cold soldering. Soldering temperature and time vary with different materials and processes. Generally speaking, the soldering temperature needs to reach about 200°C and the soldering time is usually around 2-3 seconds.
- Check the arrangement and orientation of the components: Before soldering, it is necessary to carefully check the arrangement and orientation of components to ensure that they match the markings on the board and are soldered in the specified sequence.
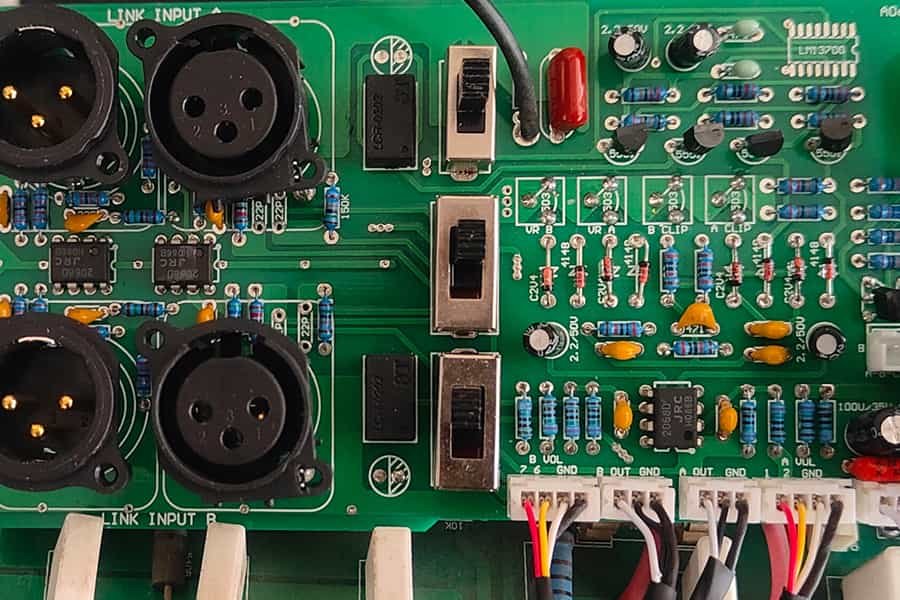
Make sure the right arrangement and orientation
- Avoid false soldering and short circuits: To prevent false soldering, make sure that there is good contact between the solder joints and the component pins and that the soldering time is kept accurate. To avoid short-circuiting, care should be taken with the distance and arrangement of components to avoid excessive proximity or overlapping.
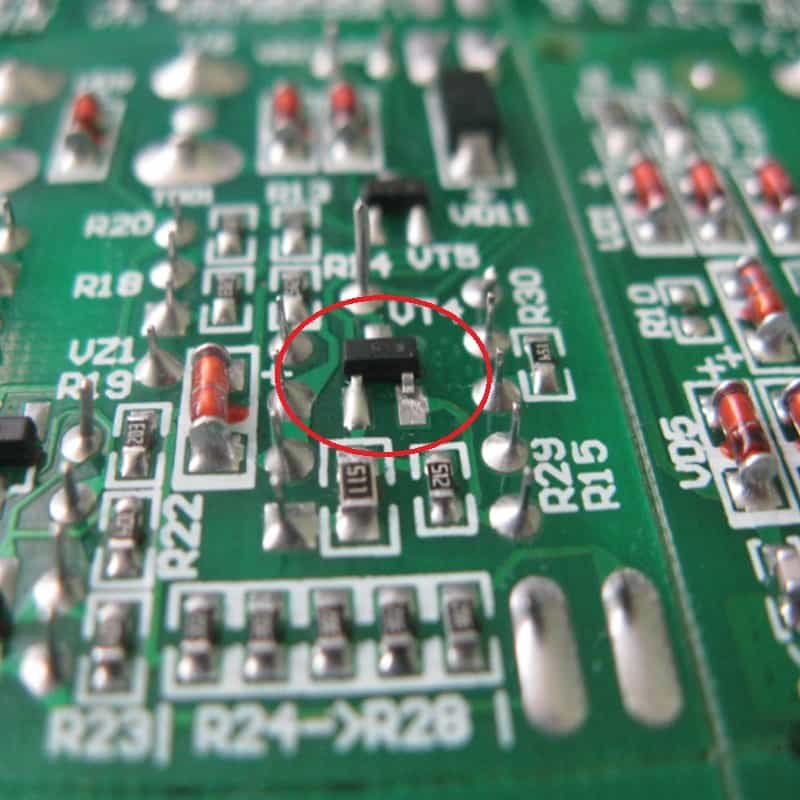
False Soldering
False soldering is one of the most common mistakes made by inexperienced employees. Therefore, strengthening soldering training to make them skilled workers is a key factor in avoiding such problems.
If the use of wave soldering equipment occurs in bulk false soldering problems, it is necessary to verify the root cause of the problem in various aspects. For example, PCB boards, wave soldering equipment parameter settings, flux, and solder material.
- Check the cleanliness of the solder joints: After the completion of soldering, if there is excess solder and flux, the surface of the solder joints should be cleaned immediately to ensure the beauty and reliability of the solder joints.
- Follow the welding specifications and safe operation procedures: When welding components, you should follow the relevant welding specifications and safe operation procedures, pay attention to the protection of eyes, skin, and other parts of the body, and avoid inhaling harmful gases and dust.
Amplifier Case Assembly
During the assembly of the circuit board into the amplifier case, it is essential to follow a specific order and requirements. This ensures that every part is correctly installed, and the connecting cables are neatly arranged without any misalignment or confusion. Additionally, attention must be given to the amplifier’s appearance and structural strength, guaranteeing compliance with design requirements and safety standards.
Debugging and Quality Testing
Debugging and testing of amplifier is one of the key steps in quality control. The following are some of the steps of debugging and testing:
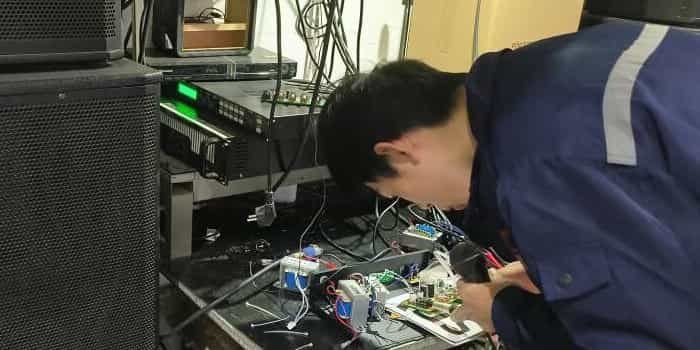
- Power Debugging: check whether the power of the power supply meets the requirements and whether the voltage meets the requirements. Also test the stability.
- Audio Input Debugging: Check whether the audio input signal (such as microphone input, USB input) is normal, including the signal level, frequency and phase and other parameters.
- Audio Output Debugging: check whether the audio output is normal, including output level, signal-to-noise ratio, distortion and other parameters. Also check whether the material of the output terminals meets the requirements.
- Protection Function Test: test the amplifier’s overload protection, overheating protection and other protection functions are normal.
- Performance Test: Conduct a comprehensive performance test, including the amplifier’s gain, bandwidth, dynamic range, distortion and other parameters.
- Reliability Test: A long aging test is conducted to check the reliability and stability of the amplifier. This includes long-time running tests, switching tests, etc.
- Safety Test: Test the safety performance of the amplifier, such as grounding resistance, insulation resistance, etc., to ensure the safety of the user.
- User Interface Test: To check whether the amplifier’s user interface is friendly and easy to use, including control panel, display, buttons, etc.
- Compatibility Test: Test the compatibility of the amplifier with other devices, such as whether it can connect and communicate normally with other devices or software in the public broadcasting system.
- Lifetime Test: Long-time working test for the audio amplifier to evaluate its life and reliability.
Quality Control Points
Component Soldering Quality
In the circuit board assembly stage, the quality of component soldering needs to be strictly controlled. This includes the quality of the soldering point, the purity of the solder, the soldering temperature and time, etc. If the soldering quality is not up to standard, it may lead to false soldering, desoldering, and other phenomena.
Assembly Order and Requirements
In the overall assembly stage, it needs to be assembled in a certain order and requirements to ensure that each component is installed in place. At the same time, it is also necessary to pay attention to the arrangement and fixation of the connecting cables to avoid misalignment and confusion.
Debugging and Quality Testing
Debugging and quality testing are key parts of quality control. It is necessary to use professional test equipment and tools to test and adjust the performance indexes of the amplifier to ensure that it meets the design requirements and user needs. At the same time, it is also necessary to record and analyze the test results to find and solve potential problems in time.
Environmental Control
The cleanliness of the workshop is another important aspect of quality control. The workshop sanitation system needs to be strictly enforced to prevent dust, dirt and humidity from affecting the amplifier. And the daily monitoring of temperature and humidity should be fully documented to meet the requirements of the production process.
Technical Parameters and Specifications
Technical parameters and specifications are important references for consumers when purchasing PA Amplifiers, as illustrated by the parameters of our public address broadcast amplifier example:
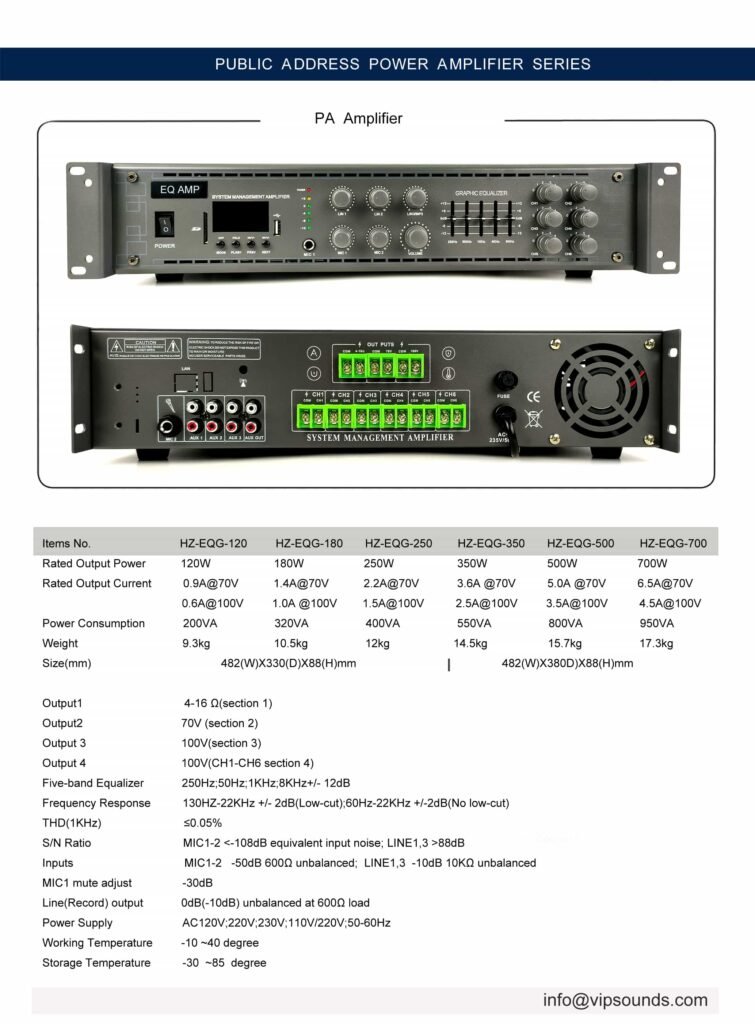
We provide high-performance PA amplifier solutions with the latest technology, and more importantly, guarantees fast delivery times and attentive service to ensure customers sufficiently benefit from our high quality and competitively priced products.
Conclusion and Outlook
Through the above three aspects, we can see that high-quality broadcast power amplifiers need to be strictly controlled in many aspects, such as material selection, production process, and quality testing. We are committed to providing customers with broadcast amplifiers with excellent performance and reliable quality to meet broadcasting needs in different scenarios.
Looking ahead, we will continue to pay attention to market demand and technological development, continuously optimize product design and production processes, and strive to improve the performance and quality of our products. Meanwhile, we will also actively explore new application areas to serve the broadcasting industry’s development better.